Management model in condition of single and small batch productions
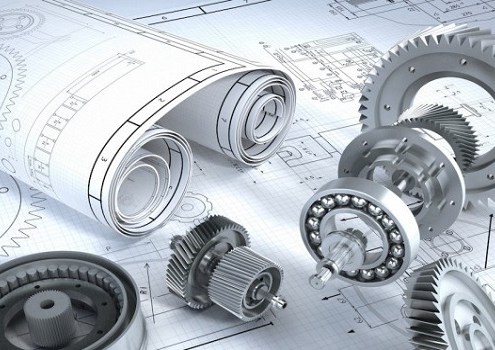
Project label
SV002
Project duration (years)
2019.-2021.
Project abstract
The industrial revolution as a new paradigm of the development of physical – cyberspace has set new requirements in the hardware, software, network, data, organizational and human aspects. Previous knowledge is becoming obsolete, and new spaces are being created for the use of new tools and methods in order to create production processes that will significantly reduce costs, speed up flow, increase flexibility, but also improve quality taking into account environmental parameters.
The answer is a company built on a business model designed to achieve maximum value by applying digital technology for customer orientation and better service through a focus on quality, price and time; giving greater importance to talent; improving productivity and increasing profits while reducing greenhouse gas emissions, reducing waste and improving value through production without stocks and defective products; improving energy efficiency and reducing average energy consumption per facility, ie bridging the continuous improvement gap between operational performance and environmental performance.
During the research, significant deviations were shown, especially in the field of individual and small-batch production, especially in production planning during the launching and scheduling process, in order to ensure production factors and fine production planning at the plant level in very short time periods.
The launching of the production is harmonized with the terms from the operational schedule and practically starts when the work order is delivered to the production and through it all the operational work documentation. The quantities of parts provided by the operational plan can be launched into production in different ways depending on the rhythm and volume of the launching. Launching volume means the amount of parts that are sent into production process into production through work order. In rhythmic production, the launching volumes are the same, but for repeated launchings, they can also vary with each other, as is the case with arrhythmical-controlled production. The distance (period) between two launching cycles is called the launching interval, and the rate of that launching is called the frequency. The launching frequency can be rhythmic and arrhythmic.
Since the planning and operational management of arrhythmic production is difficult, it should be avoided or efforts should be made to reduce the amount of variation in the volume and interval of launching. Achieving a balanced launching increases the degree of security of due dates and simplifies the tasks of operational preparation and production management.
Project aim
The aim of the project is to develop a management model that would be applicable in single and small-scale production. These types of production have proven critical due to the large number of different work orders competing in a limited set of resources at the same time. As it is expected to achieve the shortest flow today with optimal utilization of human and material resources while reducing costs and adhering to delivery times, a number of different parameters (technical, technological and organizational) have to be agreed to ensure a favourable schedule in the production process.
In addition to the standard priority rules (EDD, SPT, LOT, FIFO…), the launching process also uses tools based on operational research methods, artificial intelligence, and various combined and hybrid algorithms that have not so far shown or provided adequate responses to the launch and deployment process under conditions single and small batch production. Namely, such problems are among the so-called difficult NP problems where it is almost impossible to find the optimal solution in real time. Therefore, the challenge is even greater because besides technological ones (e.g. component or recipe, technological process, availability of resources…), the model must also include non-technological ones (customer importance, availability time and cost of materials, human resources and their knowledge, potential profits, potential penalties …) parameters.
Such a complex model should allow the creation of a multi-variant launching plan depending on the goal function set, which may be one or more dimension-defined (e.g., time, cost, schedule or combination of different). This would enable the management to choose at the given moment the most favourable (suboptimal) solution to the observed problem.